R33 GT-R フードレッジの酷いサビ
R33スカイラインの弱点を修復
フードレッジってなに?
いろいろな呼び方があるようですが、フードレッジとかストラットサポートとか言われる部位に発生した錆の修復が今回の主体作業となります。
今回の作業で初めて知ったのですが、R33ではかなり有名な錆ポイントのようです。「R33 フードレッジ 錆」で画像検索すると似たような画像がゴロゴロでてきます。
検索結果を見ると外観から想像するよりも内部は酷くサビていることが多いようだということが分かります、そんな前提知識を仕入れて車を見てみます。
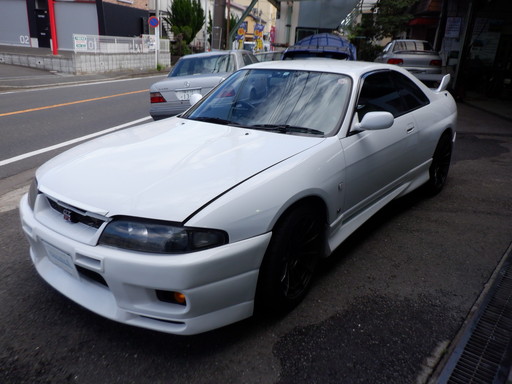
外側からはサビの様子はわからないのでボンネットを開けてみます、フードレッジに錆があると言われたのですがどうでしょう。
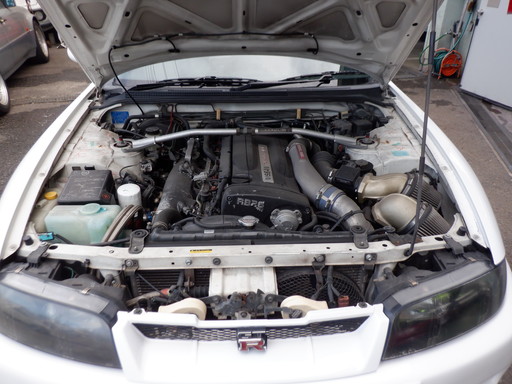
「え?錆ってこれ?」と思ってしまうくらいの錆です、拡大してみましょう。
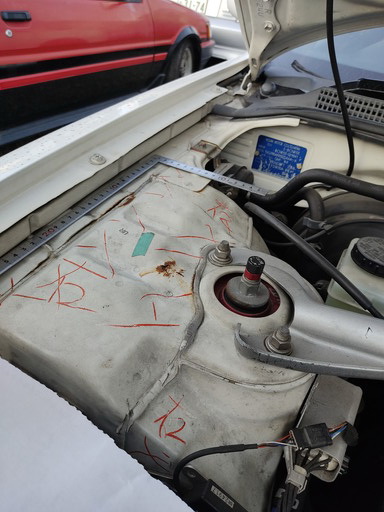
ストラットのすぐ隣に錆が浮いています、小さな浮き錆があるだけのようにも見えます、前もって画像検索で予習していなければ甘く見ていたかもしれませんがこの錆の内部ではサビこぶが成長しているのでしょう。
パネルを清掃してもう少し詳しく見てみます。
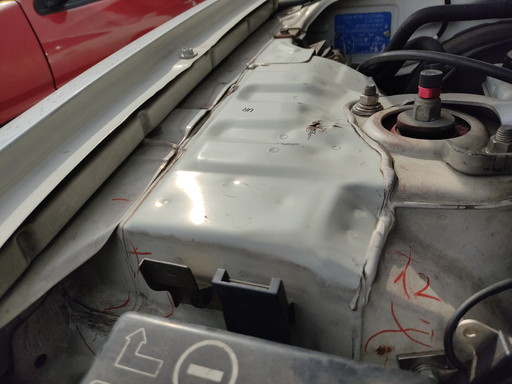
こんなにじっくり R33 のフードレッジを眺めたことはないのでフードレッジの本来の形を知りませんが、不自然な盛り上がりは内からのサビこぶだろうと思うので、復元すべき元の形状を想像しながら次はパネル自作の為に計測していきます。
フードレッジを計測
今回の計測では現車を直接定規で測るのではなく、計測したい場所を画像としてパソコンに取り込み、その画像から CAD で図面に起こして、その図面から細部の寸法を拾っていくという面倒なやり方です。
まずは現車を注意深く観察します、一見するとただ凸凹しているようにも見えますが、シャーシ等に無意味な形状というのはあまり無いので、この凹みにはどんな意味があるのか何故ここにラインがあるのかを考えていくと測る場所が見えてきます、見えるというか見やすいようにマジックで線を引いていきます。
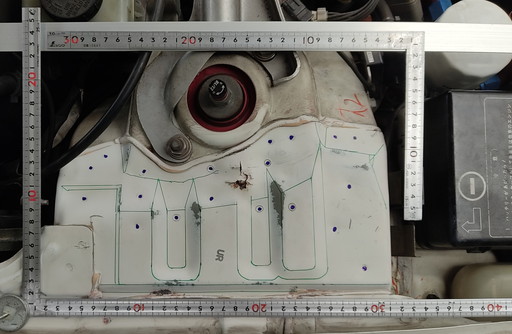
必要な形状が見えてきたら撮影して下絵としてパソコンに取り込みます、下絵画像には歪のない平行投影な画像が欲しいのですが、一般的なカメラ(スマートフォン)で撮影すると透視図の歪みができてしまいます、歪みを補正しやすいようにスケール等サイズのハッキリしている物を一緒に撮影しておくとこの後の作業が捗ります。
もしカメラだけで平行投影画像を作ろう思うなら超望遠レンズを使ってすごく遠距離から撮影すると良いらしいですがあまり現実的ではないかもしれません。
CADで作業する時に便利なのでトレーシングペーパーで原寸も写し取っておきます。もし大きなコピー機をお持ちなら写し取った紙をそのまま使って自作パネルを作っても良いと思いますが、私はいきなり作るのは苦手です、それは初めてみる立体に対して何から手を付ければ形が作れるのかがわからないからです。
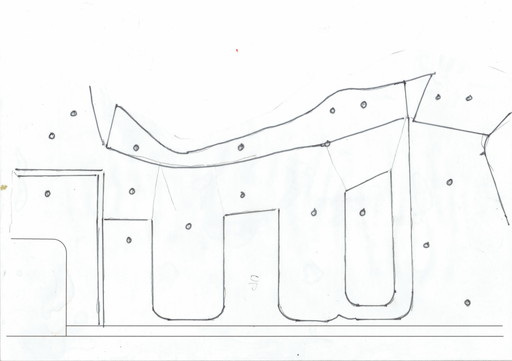
前にも書いたような気がしますが私はモノの形状を立体的に捉えるのがとても苦手です、そこで最初は形状が理解できていない状態であっても CAD で形状を図面に再構築してそれを計測していくという面倒な作業を通して、ようやくだんだんとモノが立体的に見えるようになってきます。
面倒な方法で時間もかかりそうですが、形状が理解できていない状態でいきなりパネルを曲げて試作品のゴミが増えるよりはほんの少し作業が早いです。
さて、下絵画像が準備出来たらしばらくはパソコンで作業をします。画像の歪みを補正したら CAD に画像を取り込み、写した線と寸法を合わせながら形状をトレースしていきます。
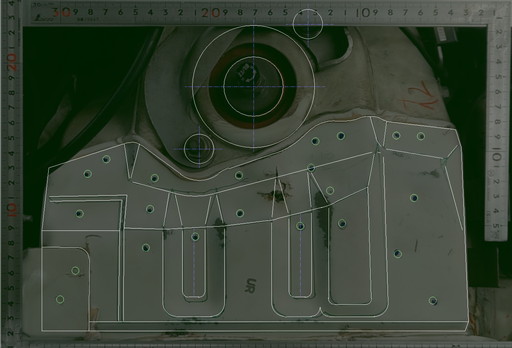
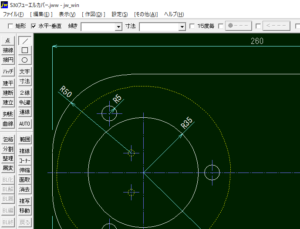
【CAD】 コンピュータを使った設計支援道具のこと/ここでは2次元汎用CADの中でも軽快な動作でみんな大好き「Jw-cad」を寸法のメモに使用/パネルの板取ではとても重宝する/操作が変態なので他のソフトと行き来するとパニックになる
これで上から見た平行投影図が出来上がりました、しかしこのトレースでは単に上面からの平行投影なので斜面の寸法を拾うことはできません、そこで次はパネルの凹凸を型取りゲージを使って写し取っていきます。
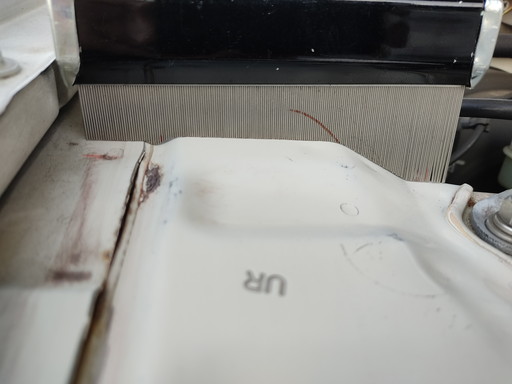
型取りゲージで測る位置は多い方が解像度は上がりますが無駄に多くしても仕方ないので面の変化する位置を何箇所か測れば十分だと思います。
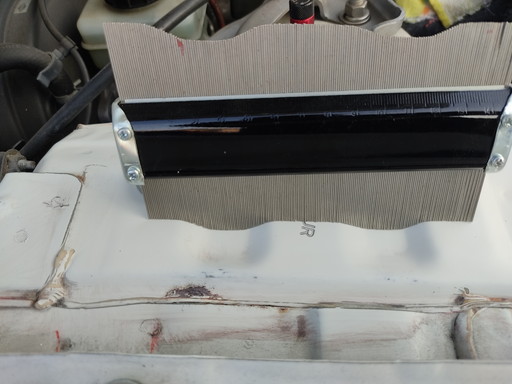
型取りゲージで写した形を自作の方眼紙に書き込んでいきます、書き込むときには基準になる位置を決めておくと後の作業が楽です、写し取りが終わったら用紙をスキャナーで読み取るかカメラで撮影して CAD に取り込みます。
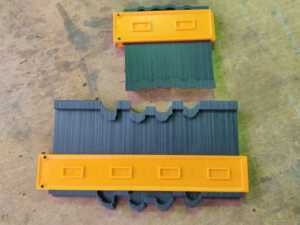
【型取りゲージ】 対象物に押し付けて形を写し取る道具/樹脂製の針は扱いが楽だが大まかな形状しか取れない/ステンレス針は細かく写し取れるが針がよく曲がる/あると助かる便利道具/ステンレス針を違う用途に流用してしまう。
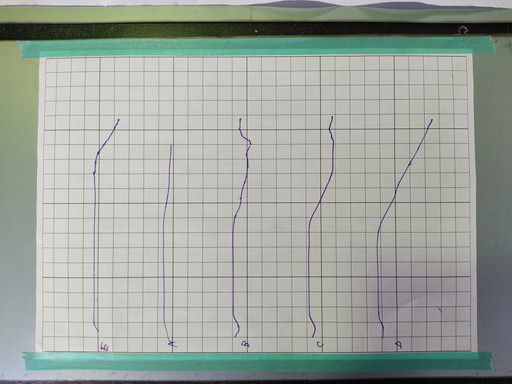
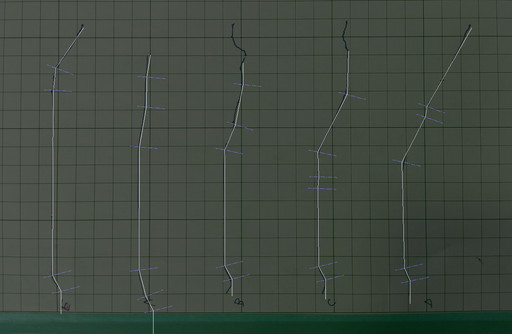
X軸方向とY軸方向両方の形を写し取ります。
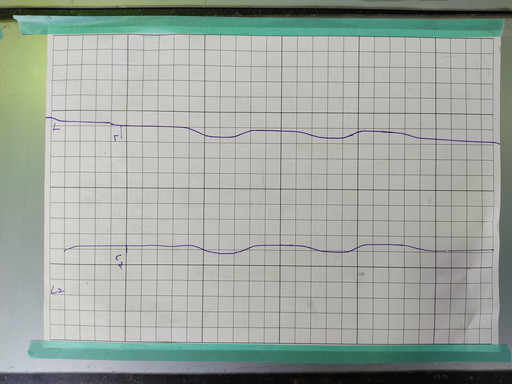
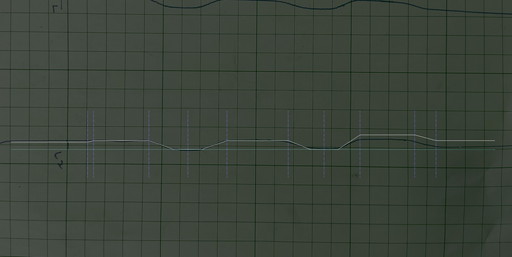
CAD でトレースをする時には必然的に基準になりそうな面や線を決めてから作業を始めます、まず基準線を決め、この基準線に対してこの膨らみは何mm上げる、下げる、曲げる、角度はコレ、長さはコレといった思考方法でトレースを進めます、そうやって作業をするとトレースが終わるころには CAD では2次元のままですが頭の中では寸法を持った立体的な形状が自然と出来上がってきますし、同時に加工方法や段取りも思いついてきます。
X軸 Y軸 のトレースが終わったらその寸法をもとに投影図を修正していきます、原寸の図面が起こせたら計測の作業は終了です。
一応寸法があっているのかを簡単に確認してみます。方法は図面をレーザープリンターでトレーシングペーパーに原寸で出力するだけです。トレーシングペーパーなので現車に書いたマジックと重ねてみてピタリと合えば正解です。
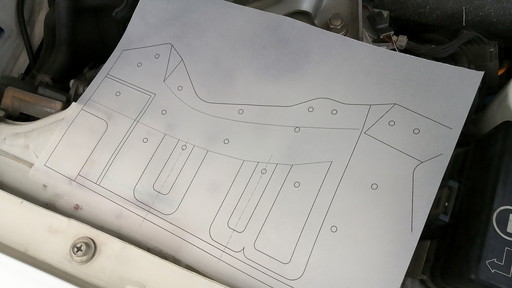
雰囲気は良さそうなので余分な部分をカットしてフードレッジに載せてみました。
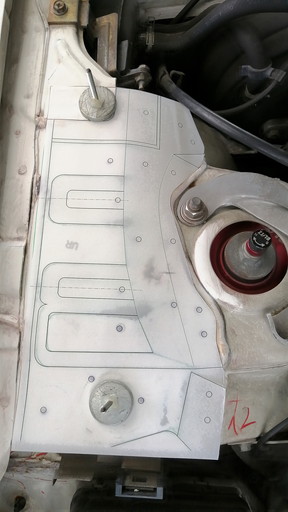
良いですねピッタリです、この出力した図面は自作パネルの基準面ということになります、この基準面に対して何mm上げる下げるという加工で凸凹の形状を作っていくことになります、この方法の利点は「あれ?ここは何mmだっけ?」となった時にいつでも必要な長さ角度を取り出せるところです。
さて実際にパネルを加工していきます。
フードレッジの板厚は何mm?
パネルを作ろうと思ったところでふと疑問、フードレッジの板厚は何mmあるんだろうか、よく切継ぎに使うのは 板厚0.8mm や 1.2mmの鋼板ですがそれよりは分厚いようです、鋼板の板厚はそんなに種類はなくて1.2mmの次が1.6mm 続いて 2.3mm 3.2mm となっています、2.3mm もあるようには見えないので 1.6mm か?わからないので先に腐食部分を切り取ってしまいましょう。
フードレッジの切り取り
フードレッジは何枚ものパネルが重なってできているので、一部のスポット溶接を剥がして作業スペースを作り腐食部分が切り取り易いようにしておきます。
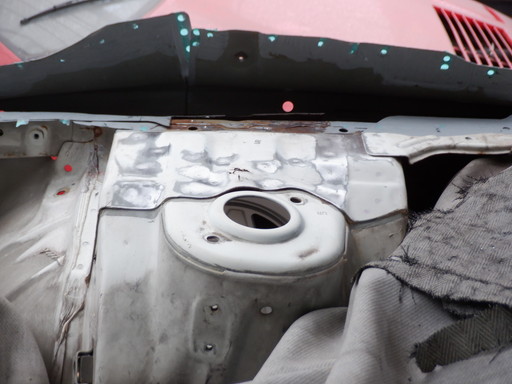
剥がしてみると中のメンバーがサビてボロボロになっていました、強度的にまずいので後で切継ぎしておきます。その他のメンバー内部にはジンクコートを塗って防錆しておきます。
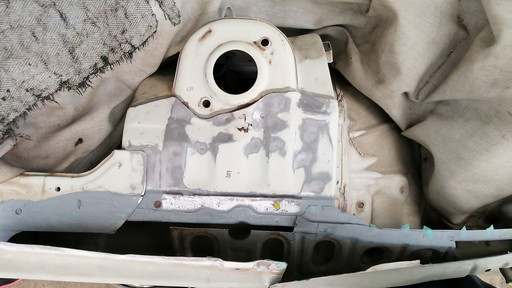
スポット溶接を剥がしてたので切り取ってみます。
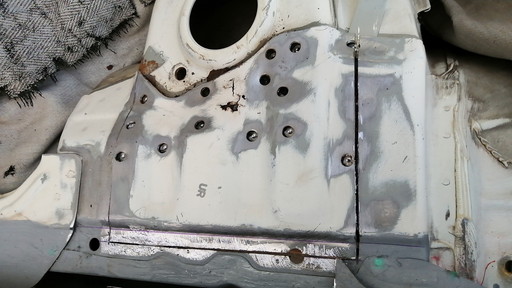
スポット溶接を揉み取ったドリルの穴から真っ赤な錆がボロボロ出てきます。
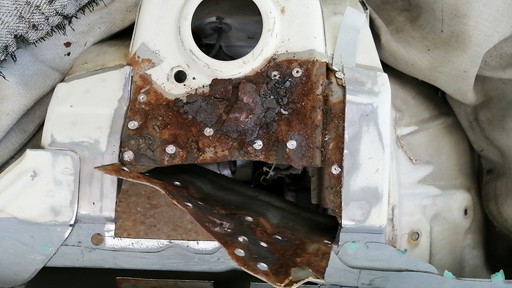
パネルを剥がすと酷い状態です、外側まで出てきていたサビこぶも大きく成長しています。あの小さな浮き錆からは考えられない程の量の錆が現れました。
巨大なサビこぶ(腐食生成物)
サビこぶをアップで見てみましょう。
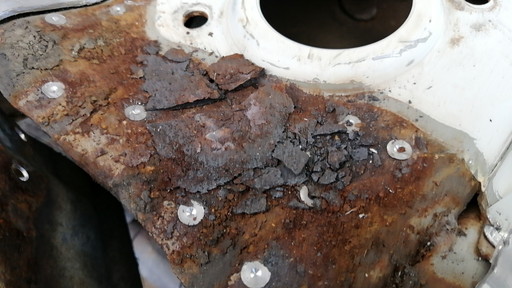
ボロボロと分離しているサビこぶが多数ありますのでワイヤーブラシで掃除してみます。
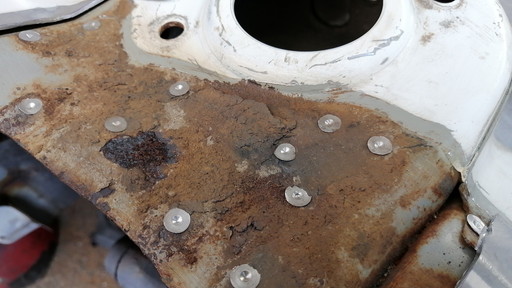
ワイヤーブラシでゴシゴシ掃除をしてサビこぶは全部取れたと思ったのですが、何やらうっすらと亀裂のようなものが見えています、他にも一部黒サビ化しているような場所もあります。
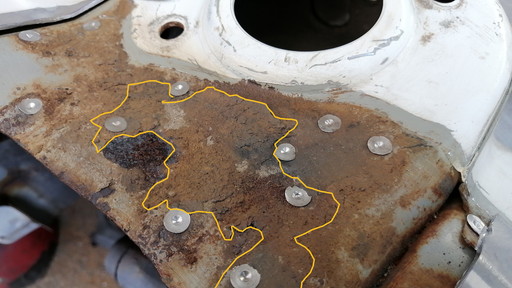
黄色で線を入れたところがパネルの亀裂のように見えるのでこの怪しい亀裂にスクレーパーを叩き入れてみます。
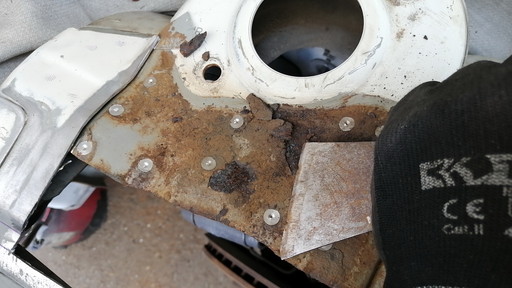
バリっと剥がれてきました。どんどん剥がしてしまいます。
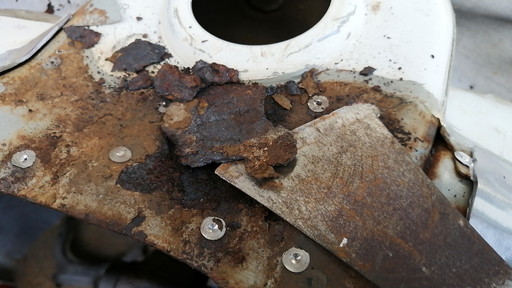
立派なサビこぶがとれました。
最初にあったコブは上のパネルのサビこぶで、今剥がれたのは下のパネルのサビこぶのようです。以前何処かでサビこぶの影響を書いたような気もするので説明はそのどこかのページを読んでもらうとして、とにかくサビこぶを取り除きましょう。
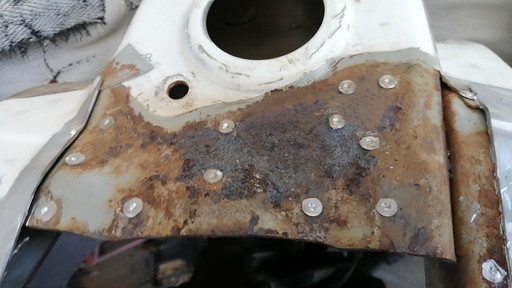
コブ(腐食生成物)がこれで全部とれました。
サビ落としとジンクコート
細かな錆も落としてパネルを清掃します。
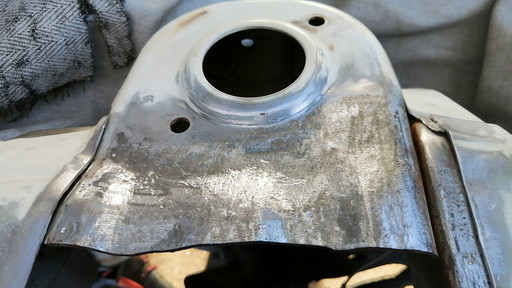
清掃が終わりました、これから自作パネルを作るのでパネルが完成して溶接する準備が整うまでの間、清掃した箇所をジンクコートで防錆しておきます。
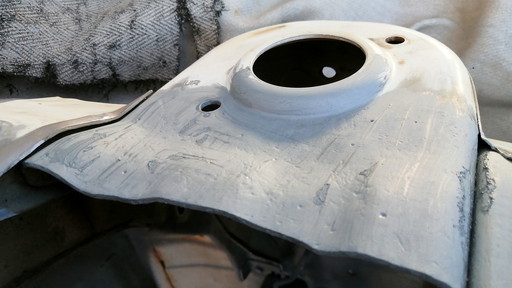
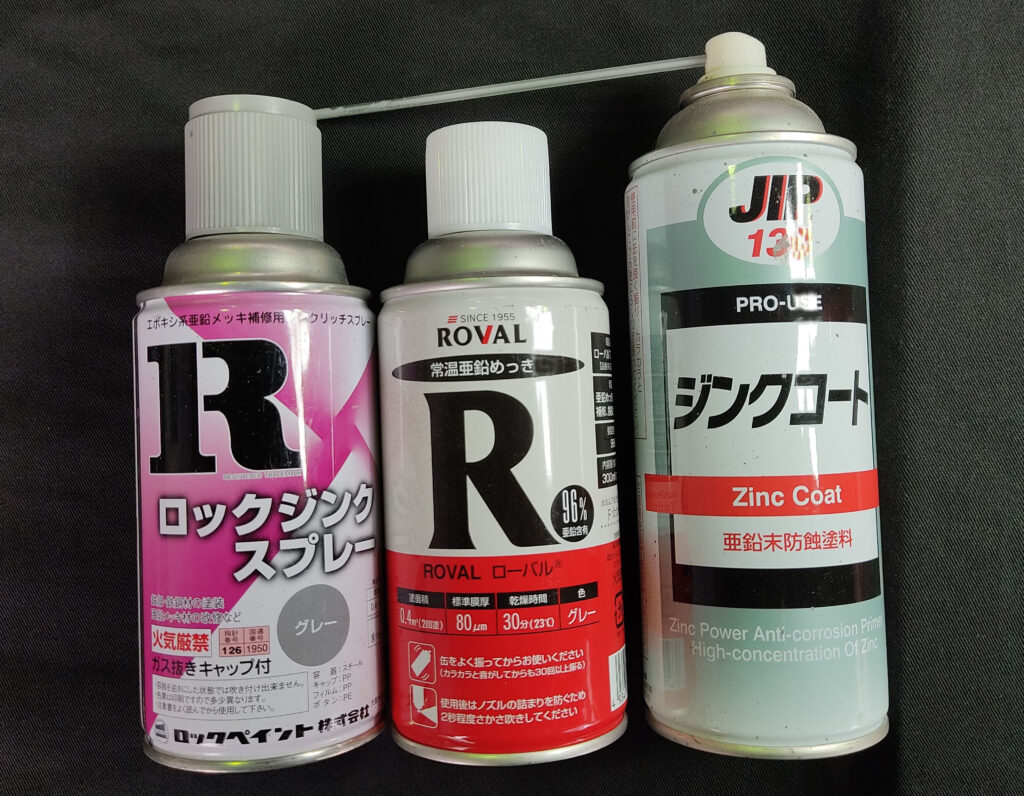
【ジンクコート】 みんな大好き常温亜鉛塗料のこと/イオン化傾向の大きな亜鉛が犠牲となって鉄板を守ってくれるサビと戦う人の強い味方/茶色いところには大体吹き付ける/上塗りができないという弱点が存在する
ジンクコート大好きな理由は実験のページに書いてあるので気になった方はご覧ください。
切り取ったパネルの観察
切り取ったパネルをサンドブラストに掛けて状態を見てみます。磨いたパネルの表面を見ていると穴が開いている以外は綺麗なものです、なんとなく穴だけ塞いでこのまま付けたらいいんじゃないかと思ってしまいそう。
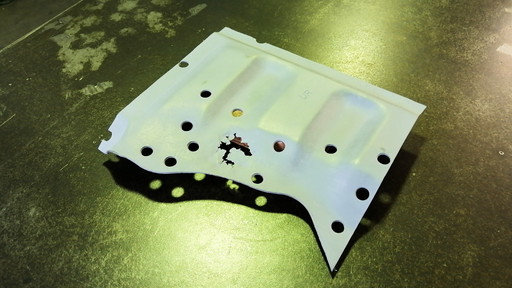
知りたかった板厚は 1.6mm で良さそう。
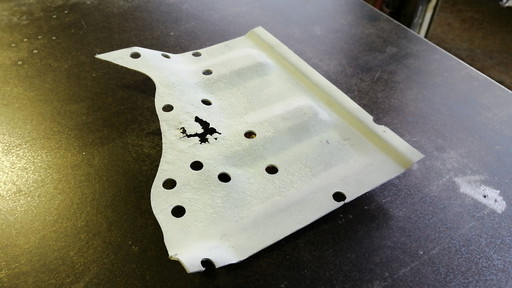
表面は綺麗でしたが裏面を見ると孔食でボッコボコなのでやはりこのままは使えません。
パネルを自作
CAD で図面にしたときに作業イメージはできているので 1.6mm の鋼板を用意したらさっそく加工していきます。加工といっても色々な厚みのフラットバー(鋼材)を使って雌型の代わりにして叩き出すだけです。
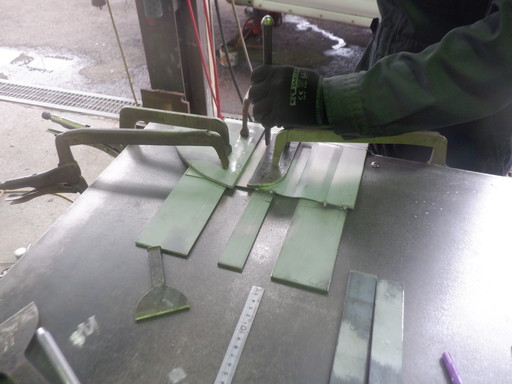
画像では 3.2mm 4.5mm 6mm のフラットバーを並べたり重ねたりしたものを作業台に直接溶接、それを雌型にしています。ザックリした説明ですが実際の作業はコレだけです、その他の形も型を作り替えて叩き出します。
図面を起こしながら考えている作業イメージは「ここは基準面から 9mm 上がるのか じゃ4.5mmのフラットバー 2枚でこの形は作れそうだな」といった感じです。
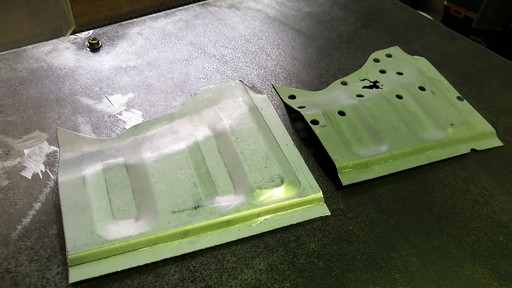
パネルは叩き出すだけではなくて、絞ったりもしながら形を作っていきます。切り取ったパネルよりも少し大きめに作っておいて成型が終わったら現車にあわせて切り出します。
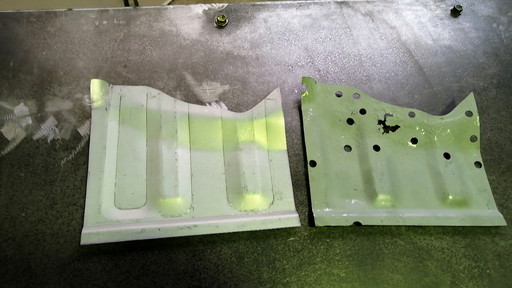
切り出しました、自作パネルの完成です。
現車に合わせて溶接準備
完成したパネルを現車に合わせてみます。
サビを落としてジンクコートを塗っていた場所は溶接に備えてウレタンサフェーサーで仕上げてあります。
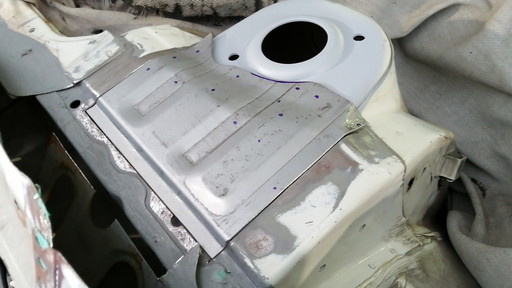
紫の点はスポット溶接の位置です、しかしこの場所をスポット溶接できるような巨大な溶接機は持っていないので穴を開けてプラグ溶接でつけていきます。
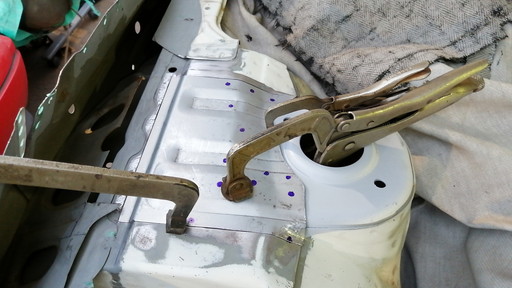
バイスで固定する場所を考えたり、溶接の為に細部を調整しておきます。
いよいよ溶接
自作パネルにプラグ溶接用の穴を開けたらいよいよ溶接します。
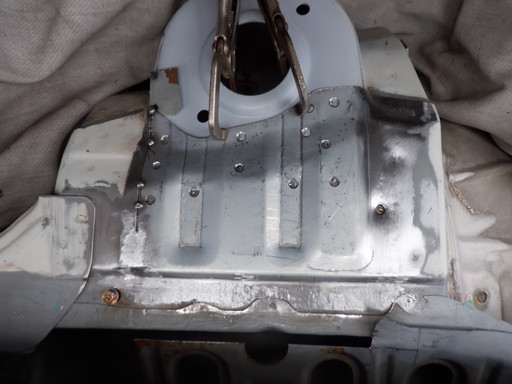
端から溶接しています。
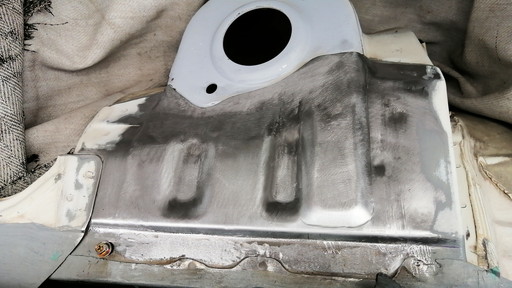
プラグ溶接の痕を削り落としたら溶接完了。
フードレッジメンバーの切継ぎと防錆
自作パネルの溶接は終わりましたが、切り取ったときに見つけたボロボロになったフードレッジメンバーの切継ぎが残っているのでその部分を作っておきます。あと自作パネルを溶接した鉄板が剥き出しの範囲は例のごとく修復が終わるまでジンクコートで防錆です。
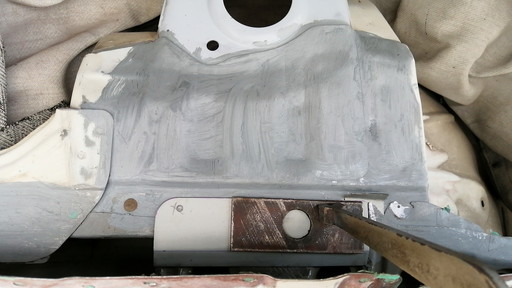
メンバーの切り継ぎは全部隠れてしまうので形は強度のみを考えて大まかに作ったら溶接します。
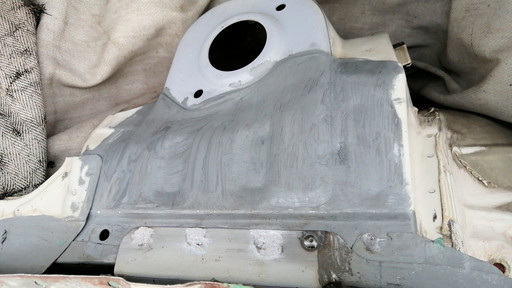
溶接が終わったのでメンバーの内部に防錆処理を施したら剥がしたフードレッジ外側を元に戻していきます。
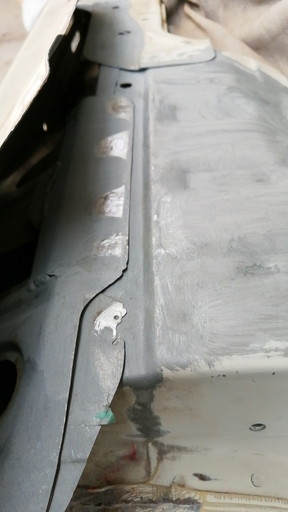
スポットを揉み取ったところはすべてプラグ溶接でつけていきます。
サフェーサーと仕上げ塗装
フードレッジの復元が終わったら全体にウレタンサフェーサーを吹いて上塗り塗装の下地を作ります。
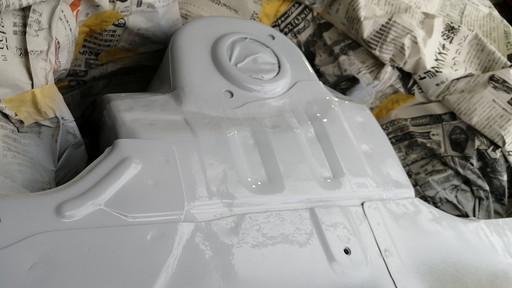
サフェーサーが乾いたら上塗りの前にパネルのつなぎ目にシーリングしていきます。
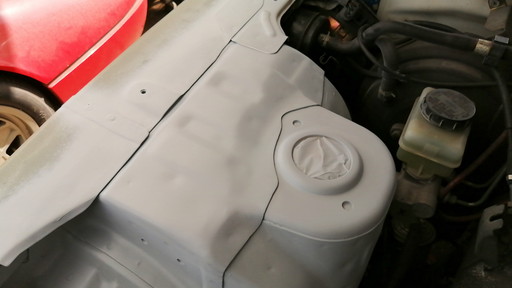
上塗り塗装と組付け
塗装が終わったらストラットやフェンダーなどを元に戻して完成です。
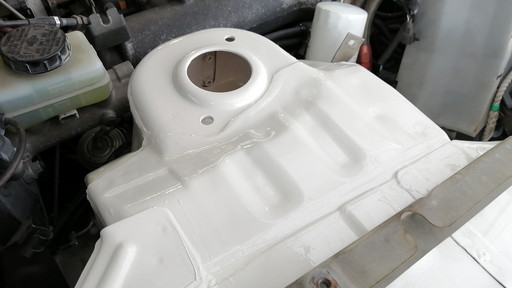
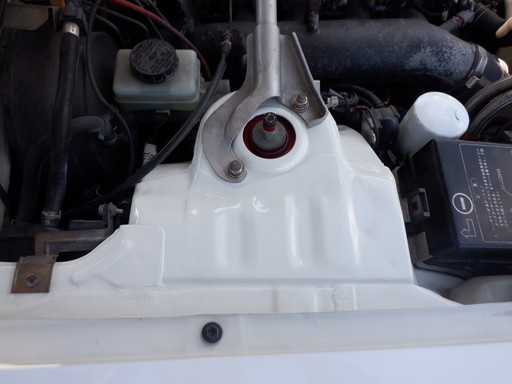
ここで紹介したのは右のフードレッジですが、左のフードレッジも同様に作りました。図面起こしは右で終わっているので形状は CAD で反転させて型を作りました。
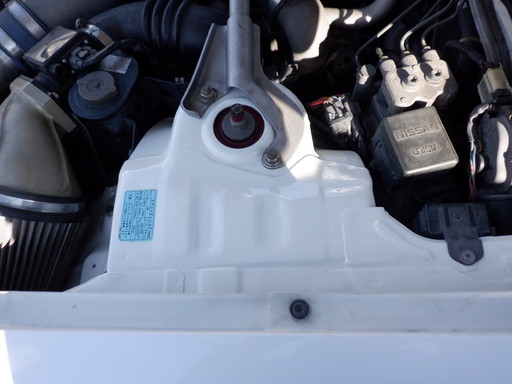
なぜサビる?
同様の腐食が多発していることは今回の作業の為に WEB 検索をして初めて知りましたが、これはどういうことなんでしょうか。R33 だけではなく R34 のスカイラインにも同じ弱点がありそうだし此れは構造的な欠陥なのか鋼材の欠陥なのか、いずれにしても見た目が小さな腐食であっても侮れないですね。
おまけ
今回は立体認識力の低い作業者が CAD を使った図面起こしと計測でなんとかフードレッジを再現する様子を紹介しました。この作業中は 2D の CAD を使っただけで立体のイメージは脳内にだけ存在するものですが、計測したものを実際に 3D でモデリングしたらどうなるのか、このページの編集しながらモデリングもやってみました。
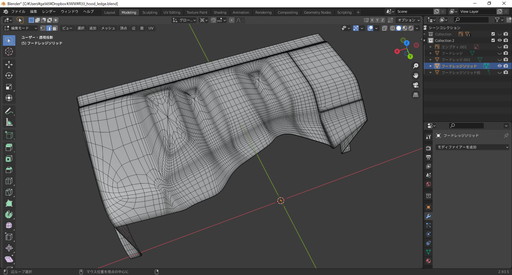
下のタイヤハウスに接続する部分の形状は正確なものではありませんが、それでも今回のフードレッジっぽいものができました。結局これもただのデータですが、もし 3D プリンターで金型を容易に出力できるようになるとパネルの自作はもっと簡単になりそうです。
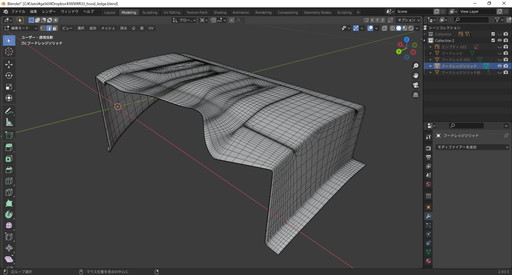